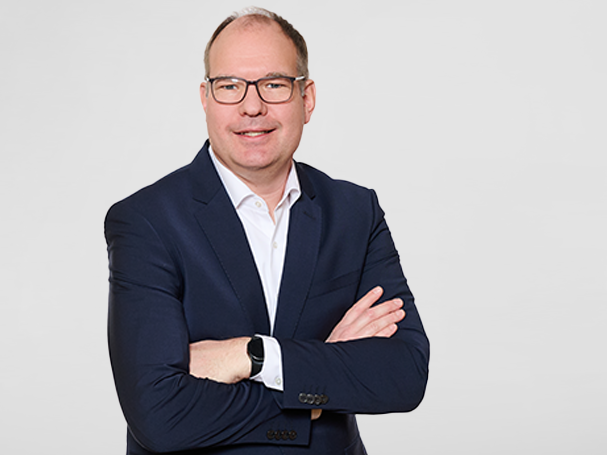
Decarbonization in energy-intensive process industries
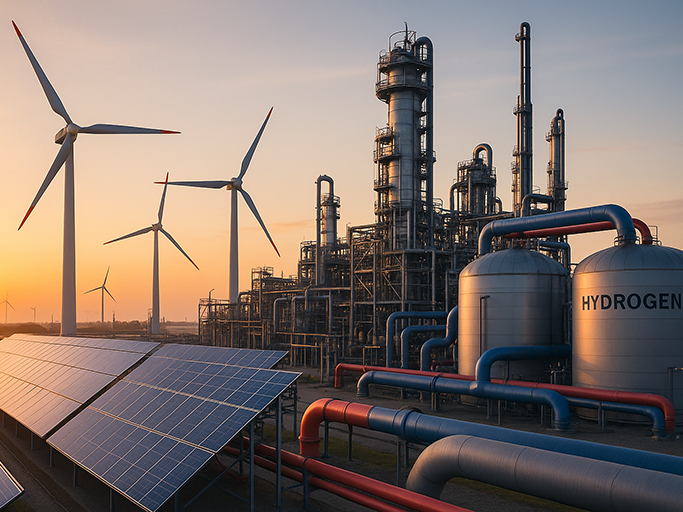
Decarbonization is a process that reduces and avoids CO2-emissions of economic activities with a special emphasis on the energy sector. The ultimate goal is to achieve a climate-neutral economy which balances unavoidable emissions by natural or technical absorption processes. However, this transition poses significant challenges, especially for energy-intensive industries. How can companies, e.g. those which produce chemicals, metals, and construction materials, effectively decarbonize their operations and value chains to meet both regulatory and economic demands?
Practical example: Integrating renewable energy and thermal storage
A compelling example of decarbonization in action is a project which built a photovoltaic (PV) park to cover the electrical energy needs of a sugar and ethanol production plant by switching to clean energy and decarbonizing operations. The excess energy generated by the PV park is stored in a thermal energy storage system and then fed into the company’s pipelines in the form of steam. Using this combined approach is commercially feasible even at today’s energy prices. By integrating renewable energy sources and their storage into an existing production infrastructure, the project demonstrates how companies can take tangible steps toward decarbonizing their operations while maintaining productivity.
Policy frameworks and regulatory pressure
While individual projects show the potential of decarbonization, their success often depends on supportive policy frameworks and supportive regulatory environments. The European Commission has set ambitious policy frameworks, such as the Green Deal Industrial Plan, the Net-Zero Industry Act, and the Fit-for-55 Package, to drive the sustainable transformation of industries. These initiatives underscore the EU’s commitment to achieving climate neutrality by 2050. Yet, companies face mounting pressure not only from regulatory requirements, such as the Corporate Sustainability Reporting Directive (CSRD), but also from rising energy costs and escalating CO₂-prices. According to scenarios by the International Energy Agency (IEA) and the World Bank, CO₂-prices are expected to increase by 10-15% annually over the next decade, depending on market and regulatory developments. That results in the challenge that investments into decarbonization must be pursued before cost of emission certificates create significant bottom-line impacts.
The role of process industries in decarbonization
The process industry—encompassing chemicals, construction materials, metals, and other energy-intensive sectors—plays a pivotal role in global decarbonization efforts. These industries account for a significant share of global CO₂-emissions, which can be categorized into three scopes under the Greenhouse Gas (GHG) Protocol:
Process-related emissions (Scope 1)
Direct emissions from chemical reactions, such as limestone calcination in cement production.
Energy-related emissions (Scope 1 & 2)
Emissions from fossil fuels burned on-site (Scope 1) and purchased electricity or steam (Scope 2).
Indirect emissions (Scope 3)
Emissions from upstream and downstream activities, including raw material production, transportation, and product use.
Given this complexity, companies must prioritize decarbonizing their entire value chain, from production processes to the use of their products and services. This holistic approach is not only essential for meeting regulatory and economic challenges, but also for driving long-term sustainability in a rapidly evolving global landscape.
Technological approaches to decarbonizing the process industry
The decarbonization of the process industry can be advanced in different ways (see image below). It is necessary and feasible to implement specific decarbonization concepts. The framework for action is at the same time extremely complex and specific, depending on the business model, product portfolio and use of technology.
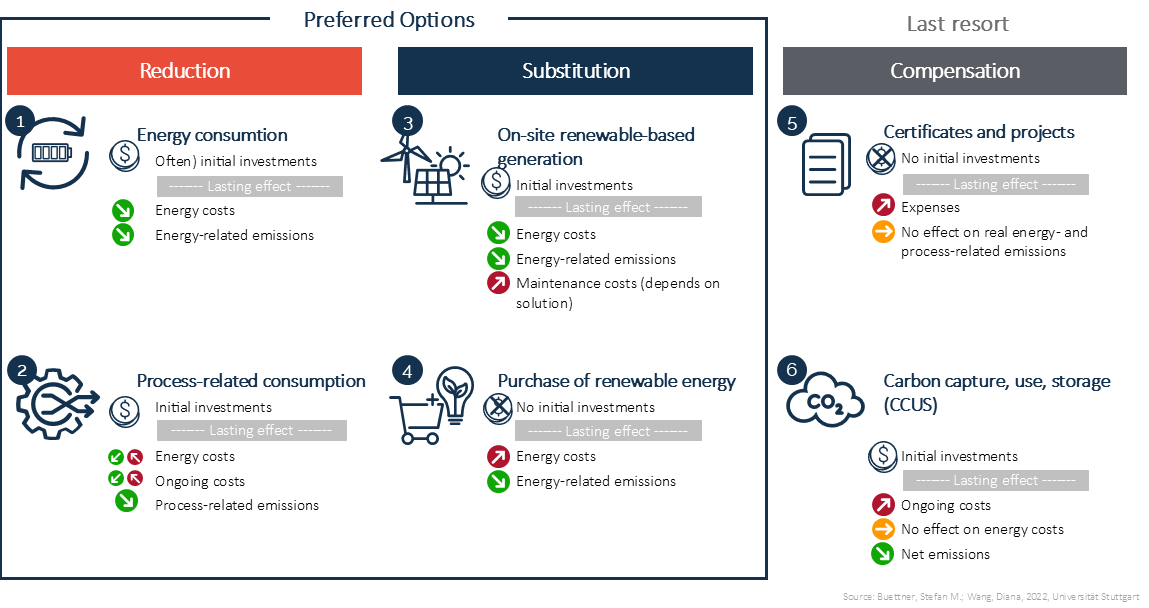
Energy efficiency measures
The optimization of energy consumption plays a decisive role in the process industry and offers great potential for reducing emissions. Measures such as the optimization of heat exchangers in chemical plants, improvement of distillation processes or the introduction of heat recovery systems in high-temperature processes can lead to considerable savings. Modern process control systems and sensor technology help to precisely control the use of energy and minimize losses. Efficiency measures often offer the best cost-benefit ratio, as they upgrade existing infrastructure and result in rapid savings.
Energy transformation
The direct use of renewable energies is particularly challenging in the process industry, as a continuous energy supply and high temperatures are often required. Nevertheless, the use of renewable energies such as solar, wind and geothermal energy is a key lever for decarbonization. Electricity generated from solar and wind power plants can be used for energy-intensive processes such as electrolysis or electrical heat generation. For example, electric boilers or electric arc furnaces could replace fossil fuels. Geothermal energy in turn offers a stable and long-term source of process heat in industries such as the chemical and paper industries. As renewable energies are often dependent on the weather and time of day, energy storage systems are frequently used. Excess heat is stored using thermal storage systems and can be made available as an energy source as required. Battery storage systems can smooth out the electricity demand in systems with fluctuating production and enable a flexible energy supply. In some cases, despite the storage of renewable energy, it is still necessary to supplement the grid supply, but this can be significantly reduced using renewable energies.
Use of green hydrogen
Green hydrogen produced by electrolysis using renewable energies offers enormous potential for decarbonizing key industrial processes. In the chemical industry, for example, hydrogen could completely replace fossil raw materials in ammonia synthesis. Ammonia is an essential raw material for fertilizers and other chemical products, and switching to green hydrogen would significantly reduce emissions from this process. Further, green hydrogen also plays a key role in steel production, as it enables the transition from the traditional, carbon-intensive blast furnace process to the direct reduction process. The Direct Reduction Iron (DRI) process uses hydrogen instead of coke to reduce iron ore, which can virtually eliminate CO₂-emissions.
Overall decarbonization requires a holistic and structured approach that starts at different levels. The challenges lie not only in technological implementation, but also in the transformation of business models, politics and society to foster sustainable change.
Economic and financial challenges and opportunities
The decarbonization of process industries is one of the most important transformation tasks of our time. However, the sometimes disruptive nature of this transformation poses several challenges.
One major challenge is the cost of decarbonization. Many implementation measures require considerable investment, be it in the development and use of renewable energy sources, the implementation of energy-efficient technologies or the adaptation of production processes. Companies are therefore faced with the challenge of coping with high costs for new technologies, uncertain CO₂-price developments and rising energy costs. Cost-benefit analyses are an essential measure for identifying decarbonization strategies with the greatest economic and environmental benefits. In addition, financing models such as green bonds, public-private partnerships or government funding programs can help to overcome financial hurdles. At the same time, early investment in low-emission technologies result in competitive advantages, for example through climate-friendly products or access to new markets.
Despite the challenges, decarbonization also offers companies in the process industry an opportunity to remain competitive in the long term through innovation and strategic adjustments and to benefit from a growing market for sustainable solutions.
Strategies for implementation
An implementation plan for decarbonization begins with a comprehensive inventory of the carbon footprint to identify emission sources and priorities. Quantifiable and achievable decarbonization targets are then set. Building on this, a strategy is developed with clear measures, timetables, responsibilities and resource allocations, which includes renewable energies, energy efficiency or sustainable supply chains, for example. Regular reviews and reports are essential for success to assess progress and adjust. Transparent communication about decarbonization targets and progress strengthens the trust of stakeholders and positions the company as a committed player in climate protection.
ConMoto and Horn & Company have extensive experience in supporting corporate ESG transformation processes. Our expertise spans the entire spectrum, from the development of general sustainability strategies to the concrete implementation of decarbonization measures. With our support, we will define your appropriate decarbonization implementation plan and help you realize your decarbonization strategy.