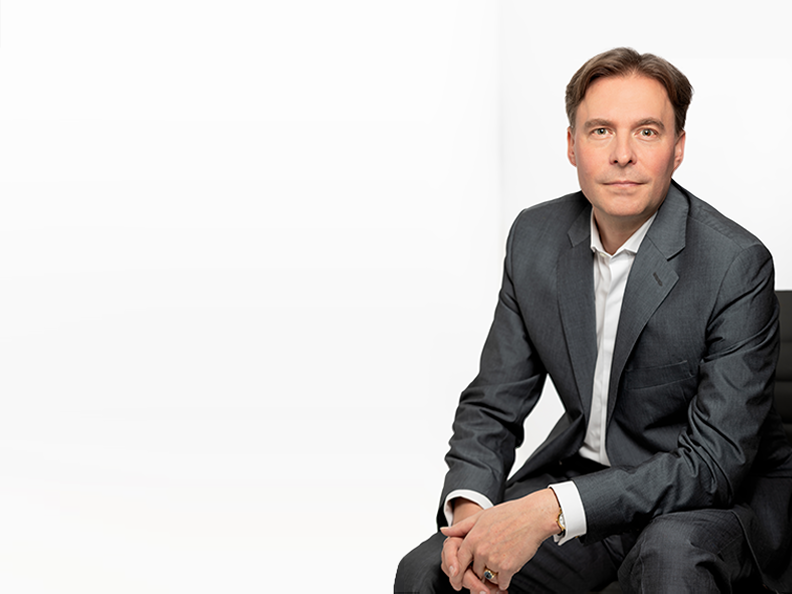
Holistic automation of manufacturing processes

Manufacturers are forced to reduce costs by competitors, technological progress and environmental regulations
The manufacturing industry is in a state of flux: competitors working at lower costs, new technologies, stricter environmental regulations and changing consumer behavior are challenging many sectors and forcing producers to drastically reduce their manufacturing costs. The automotive industry in Europe is under particular pressure. In this article, we look at the reasons for the cost pressure and cost-cutting strategies that are helping manufacturers to succeed in a highly competitive market environment.
Europe's automotive industry under global competitive pressure
The announcement by Oliver Blume, CEO of VW and Porsche, was quite something: within three years, Volkswagen plans to launch a new entry-level electric car for around 20,000 euros - “Efficient and effective - with Europe Speed.” The plan can be seen as a response to BYD's announcement that it will sell its entry-level electric car “Seagull” in Europe next year for a price of less than 20,000 euros - and that's after customs duties. This news at the latest has shaken up the industry.
The price war has been on the cards for years. Tesla has reduced prices by between 16% (Model 3) and 33% (Model X) since 2022. The tariffs in the USA and planned EU tariffs on electric vehicles from China can at best delay the price war, but they cannot avert it.
Adjusting production systems to secure margins is crucial for future success
Price competition in the VUCA world is nothing new. Most aspects have been known for years. What is new is the way in which they are being shaped. Three factors in particular are especially important and will continue to gain influence in the coming years and become decisive for the success of European suppliers:
Factor 1: Low margins
In the global price competition, OEMs are facing rising costs for personnel, raw materials and energy. This is leading to further declining margins, particularly for German automotive suppliers, which were already at the bottom of the global league table in terms of profitability in 2023 with an average EBIT of 3.9%.
Factor 2: Skills shortage
A lack of skilled workers is increasingly causing output losses and making planning and flexible personnel adjustments more difficult.
Factor 3: Great uncertainty for planning
Long-term planning reliability, previously one of the major advantages of the automotive industry, is becoming less and less important. Delayed start-ups, last-minute changes and daily changing call-offs, on the other hand, are becoming the norm.
Efficient & flexible production system to ensure profitability
While the factors described above overtax traditional manufacturing systems, they also highlight the further development that is necessary in order to be successful in the VUCA world. In high-wage regions in particular, a new approach is needed to reduce manufacturing costs and automate production processes. Automation should take the entire value creation system into account and not just improve sub-processes.
Goals of automation
- Increase efficiency and productivity
- Reduce labour costs and required skilled workers
- Minimize errors and waste
- Improve quality and reliability
- Optimize use of resources
- Shorten throughput times
- Flexibility and adaptability
- Save energy
The automation should be flexible and scalable in order to be able to adapt to changing call-offs quickly and cost-effectively. Once defined, a standard production module can be implemented quickly (to minimize investments and depreciation during ramp-up) or scaled up within a very short time (to reach the collection line).
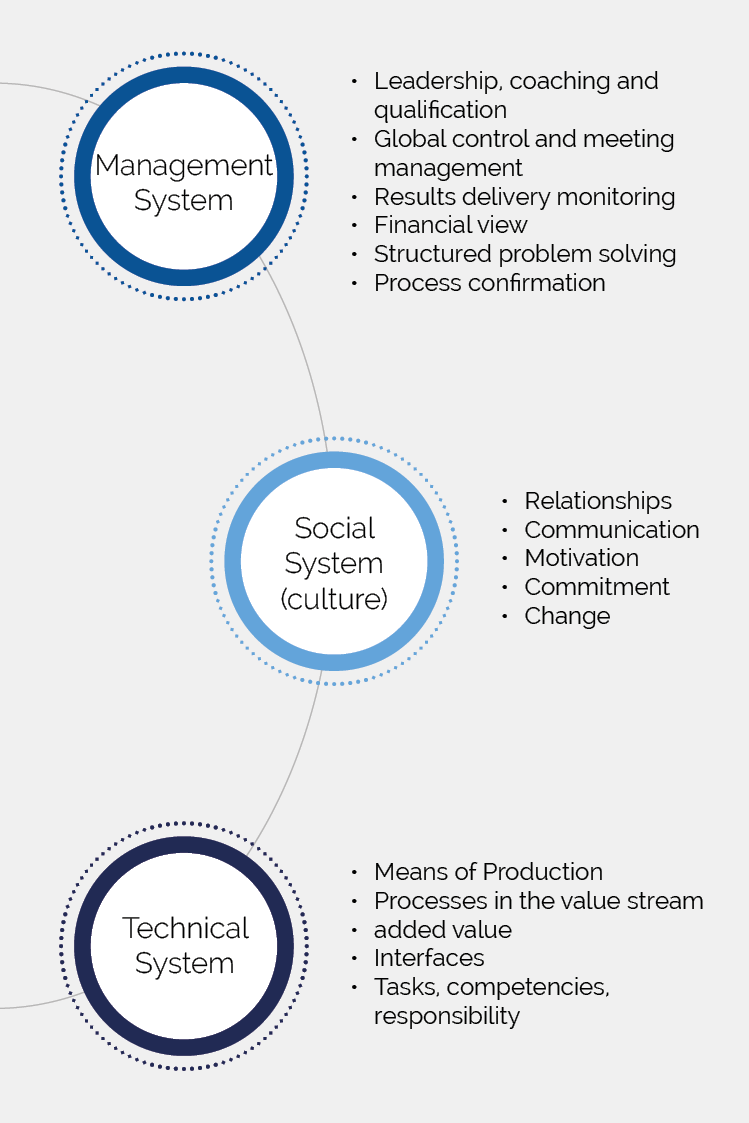
It is important to note that the automated system, the technical system, the management system and the organizational culture must be harmoniously coordinated (see figure). This means that if the degree of automation in a production facility is significantly changed, the management system and organizational culture as a social system must change accordingly.
.
Based on these principles, the Automation methodology got developed by us from decades of experience in the design and optimization of production systems and successfully implemented it with our customers
In the first step, the methodology uses the Automation-ScoreTest© to analyze the current status of automation in the customer company. Together with an interdisciplinary team from the areas of production, logistics and manufacturing engineering, a methodologically sound self-assessment of the current state of the technical, management-related and social systems is developed. Under the methodical guidance of elements such as value stream analysis and design as well as scoring based on best practices and supporting key figures are used.
In the next step, the customer-specific requirements for the production system are identified and the optimum degree of automation is defined.
An experienced team guides you through the methodology from analysis, economic evaluation and design to successful implementation.
In the next step, the customer-specific requirements for the production system are identified and the optimum degree of automation is defined.
An experienced team guides you through the methodology from analysis, economic evaluation and design to successful implementation.
It is important to avoid common pitfalls and to focus on the following principles:
- Further development of all three systems, in particular the corporate culture
- Structured selection process and selection of the right supplier
- Optimum technical design, taking into account core aspects such as intra-logistics, maintainability, etc.
- Professional risk management
Important elements that are dealt with as part of the Automation methodology:
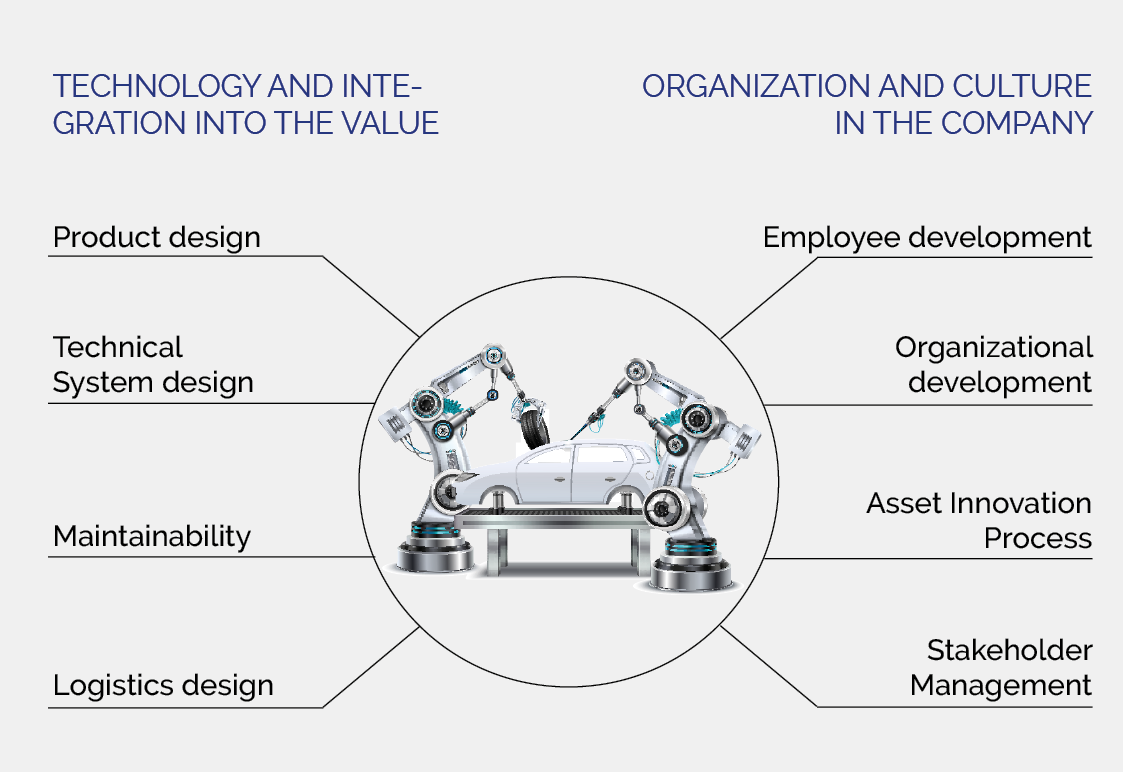
Furthermore, the focus is always on time-optimized implementation with clear milestones. Speed is of the essence, as the effects of the factors mentioned reinforce each other over time.
European manufacturers must position themselves correctly now in order to be successful in the fierce price competition of the coming years. The Automation methodology can reduce manufacturing costs by up to 15 percent and thus make a significant contribution to competitiveness in a globalized market environment.