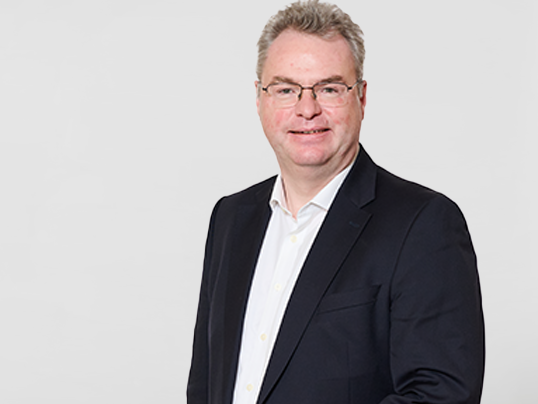
Cost deployment - creating added value instead of just reducing costs
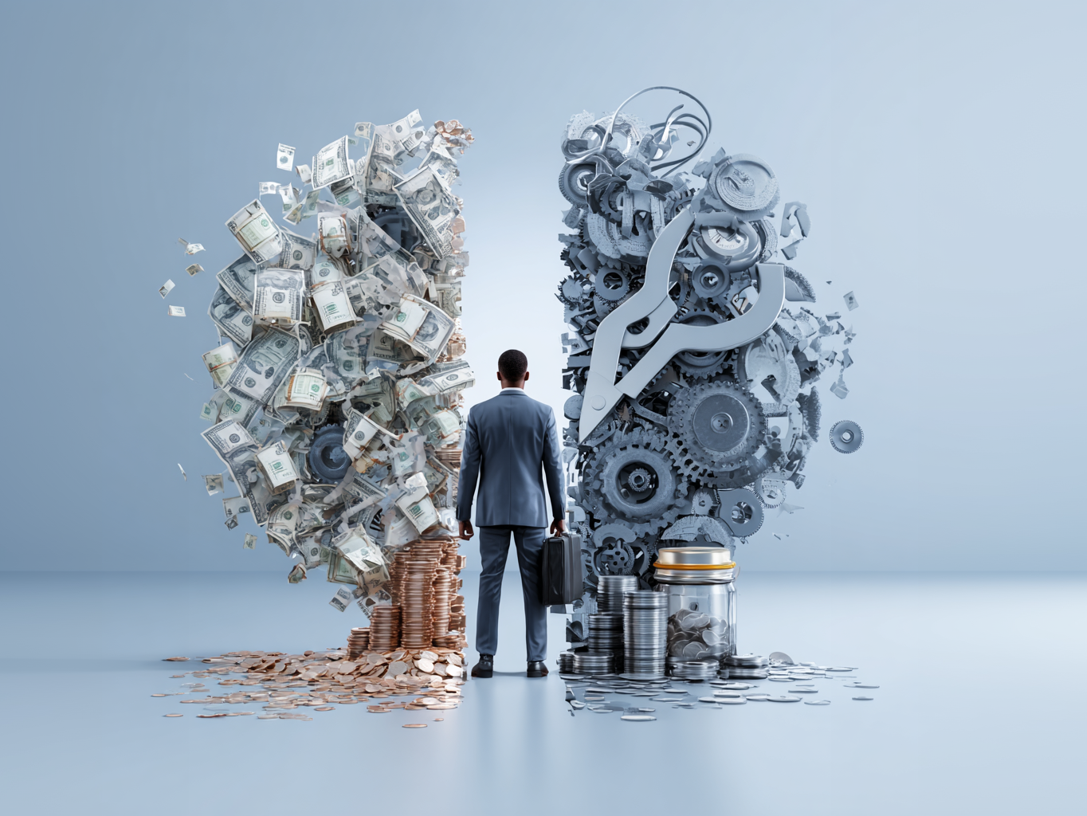
In an environment of increasing complexity and pressure on margins, traditional cost reduction is no longer enough. Cost Deployment offers companies in the automotive, mechanical engineering and process industries a structured, strategic approach to the targeted reduction of waste and non-value-adding costs while maintaining customer value.
why classic cost reduction is no longer enough
In an industrial world characterized by variant diversity, short product life cycles and high customer expectations, companies quickly come under pressure: quality, speed and efficiency are demanded simultaneously. Traditional cost-cutting measures - such as linear budget cuts or across-the-board savings targets - often fall short. In the medium term, they risk competitiveness and create internal tensions.
Cost Deployment takes a different approach: The objective is not saving its own sake, but targeted reduction of non-value-adding costs - across all functions and always with focus on the customer.
What is cost deployment?
Cost Deployment is a method from the lean tool box that aims to make costs visible, to understand where and why they arise and to take measures to reduce them sustainably.
The focus is not exclusively on short-term savings, but also on sustainable improvement:
- Which cost components really contribute to differentiation and customer benefit?
- Which wasteful practices and routines have a negative impact on quality or delivery reliability?
- Which functions cause high costs without increasing customer value?
Cost deployment provides fact-based answers to these questions - and thus creates the basis for well-founded decisions on investments, changes and prioritization.
our approach: cost deployment as a company lever
At Horn & Company, we use Cost Deployment not only in the production environment, but end-to-end along the value chain - from planning to production and logistics. The goals of Cost Deployment are
- Creating transparency about how costs are incurred
- Prioritization of improvement measures based on potential cost savings
- Linking technical losses (e.g. machine failures, rejects, downtime) with financial consequences
- Sustainable increase in efficiency through targeted investments and improvements
A seven-stage approach has proven its worth:
A. Target definition
We start with a detailed analysis of the overall cost structure (e.g. COGS) and define a company-wide savings target - based on benchmarks, top-down targets and strategic priorities.
B. Loss analyses
With the help of structured shop-floor assessments and lean tools, we evaluate processes regarding the seven classic loss types - overproduction, waiting times, transportation, overprocessing, inventories, movement and errors.
C. Root cause analysis
Losses are analyzed causally, using root cause matrices, which e.g. trace quality costs (scrap) back to their causes (e.g. set-up errors, unstable processes). We also consider losses in the indirect areas. Benchmarks with the ratio of indirect to direct FTEs show indicative fields of action. Alternatively, we use process-driven benchmarks via our Activity Rader, in which the working hours per process step are evaluated. This creates transparency and prioritization.
D. Monetization
Losses are translated into financial potential. We cross check process data with quantity and cost data to develop reliable business cases which are crucial to management decisions.
E. Adapting lean methods to individual requirements
We make targeted use of proven lean methods - including SMED, TPM, 5S, Kaizen and standardization. In the indirect areas, we apply methods such as process mining or the design of shared service centers. Always adapted to the conditions on site.
F. Tactical implementation plan
The measures are bundled in a tactical implementation plan - including responsibilities, resource requirements, milestones and timelines.
G. Progress and impact controlling
We measure progress and financial impact transparently: with monthly reporting and degree of implementation (DoI) logics that combine implementation, sustainability and impact.
Case Insight: Tier 1 supplier
A leading supplier was faced with the challenge of eroding margins. In the course of the project, we identified the following problem areas:
- Unstable production planning with a high number of variants
- Fragmented logistics processes, sometimes with express or partial deliveries
- Insufficient quality assurance in production, logistics and maintenance
- High data availability - but questionable data quality
- Strong operational management commitment, little structured problem solving
Our measures:
- Analysis and visualization of weak points and KPI gaps
- Development of an effective shop- floor management system
- Stabilization of planning (larger batch sizes, better material connection)
- Introduction of structured problem-solving processes and coaching for managers
Results:
- Direct personnel costs reduced by 16 %
- Material and scrap costs in the paint shop reduced by 32 %
The overall added value
Cost Deployment has an impact far beyond short-term savings:
- Cross-functional cooperation is promoted - e.g. between production, logistics, quality and maintenance
- Reduction of non-value-adding activities
- Customer feedback can be incorporated in a more targeted manner, leading to higher customer satisfaction
- The basis for further initiatives such as digital transformation, zero-based budgeting or performance management systems is created
Cost deployment is not an operational savings program, but a strategic lever for realigning value creation. It is a central component of modern competitive strategies, particularly in sectors such as automotive, mechanical engineering and the chemical industry - where customer orientation and operational excellence are crucial to market success.