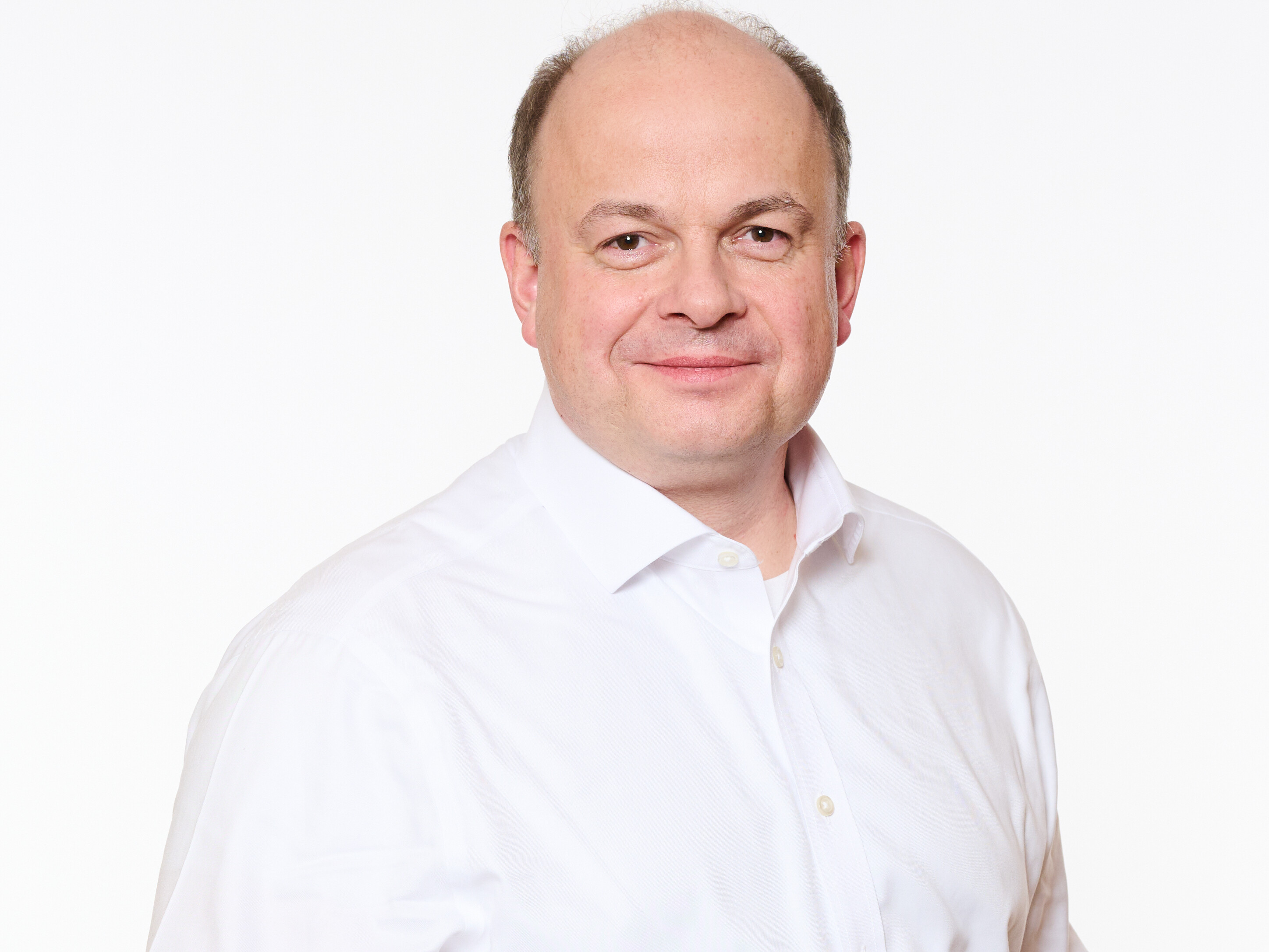
The future of glass roofs in the automotive industry: How we doubled the yield of high-tech panoramic roofs
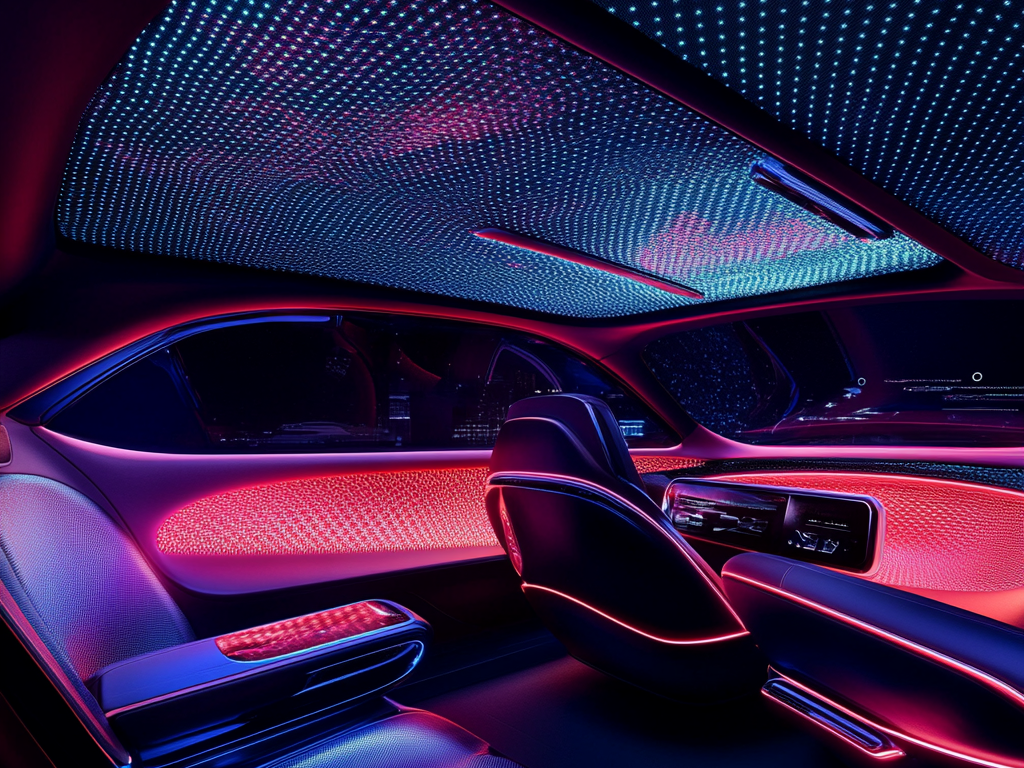
The automotive industry is undergoing profound change. With the rise of electromobility, autonomous driving and increased safety requirements, innovative vehicle concepts are increasingly coming into focus. A central element here is the panoramic roof. Glass solutions with switchable properties, such as PDLC technology (Polymer Dispersed Liquid Crystal), which switch between transparent and milky or generate other images at the touch of a button, offer manufacturers completely new possibilities. Glass roofs are gaining in importance as they improve design and comfort, visually enlarge the interior and offer passengers a customizable atmosphere. Especially in electric vehicles, which often offer more spacious interiors due to the lack of combustion technology, glass roofs complement the modern, future-oriented design. With the spread of e-mobility, equipment variants with glass roofs as a central element will also increase significantly.
Technological challenges with glass roofs
For glass manufacturers the development of panoramic roofs, however, brings with it a number of technical challenges. In addition to the central issues of flexibility, breaking strength and optical quality, there are now also difficulties such as:
- Dynamic and static deformation - Deformations can occur due to thermal and mechanical loads.
- Influence of packaging and storage - Improper handling can lead to micro-defects or stress fractures. Glass jars can also change their form due to incorrect packaging
- Processing of PVB-films - Glasses are bonded together using the synthetic resin polyvinyl butyral (PVB) . The possibility of changing the form of this laminate, opens up new optimization potential, but also poses challenges in production.
The change from laminated safety glass to partially toughened laminated glass
There is a clear trend in glass production: standard laminated glass is increasingly being replaced by part toughened laminated glass. This requires a change in production technology, with a trend towards single press bending. This brings with it specific challenges:
Increased flexibility of the glass
The change in the bending process leads to different stress constellations in the individual glass panes and the laminate, which also has an effect on flexibility.
Changed properties of the laminate and the PVB film
The interaction between glass and PVB is temperature-dependent and can lead to additional stresses in the laminate
Special requirements for transportation and packaging
Packaging design influences the dimensional stability of the end product and supports smooth installation in the vehicle body
Our consulting approach: glass know-how meets hands-on mentality
We have brought our extensive expertise in the field of glass and our hands-on mentality to bear in advising a leading manufacturer of panoramic roofs. Our approach was clearly structured:
- Analysis of the process chains - Identification of weak points in production.
- Development of individual solutions - Optimization of press bending machines and lamination processes, through adaptation and optimization of parameters and hardware and thus the improvement of geometry.
- Implementation of yield improvements - Through specific adjustments, we were able to improve the total Yield by 65% and for several High-runner products from 25% to over 50%.
- Use of "Design of Experiments" as a problem-solving method - DOE is a structured process model for the rapid identification and elimination of problem causes, when classic tools such as an 8D report or Ishikawa diagram are no longer sufficient.
- Optimization of molding processes - More efficient sealing experienced for reduction of glass breakage from 30% to below 10% and process-specific yield increase from 50% to 85%.
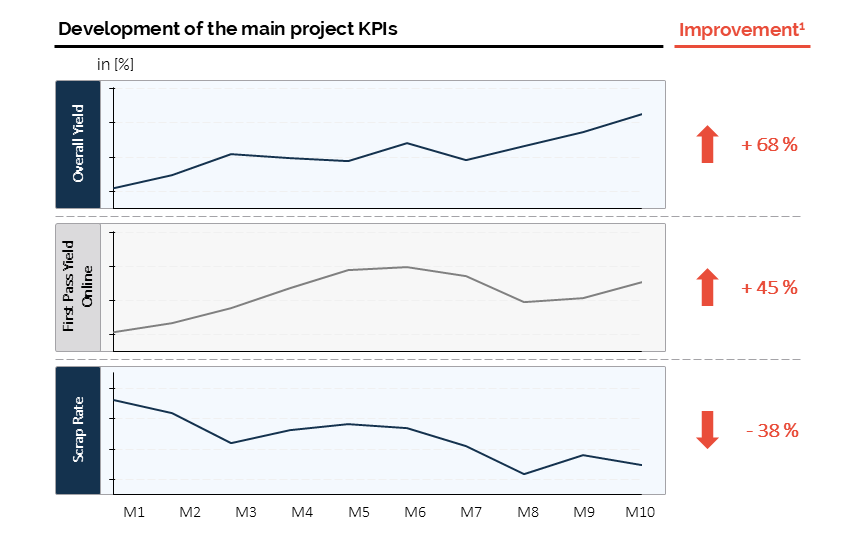
The added value for our customers
Glass producers benefit from our unique consulting approach in several ways:
Faster problem identification
thanks to our outside-in-perspective and industry experience.
Higher productivity and efficiency
through targeted improvements in production, tailored to partly unique processes.
Sustainable process optimization
through structured root cause identification with DOE.
Our work has shown: With the expertise, the right measures and the right mentality , significant increases in efficiency can be achieved even in highly complex production environments. The success of this project confirms our approach - and underlines our expertise as a strategic partner in the glass industry.